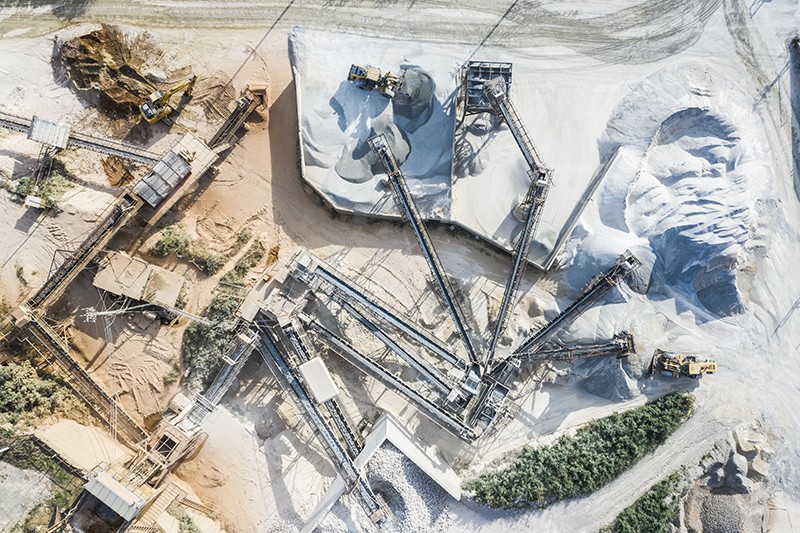
गगनचुम्बी इमारतों, बांधों, पुलों तथा गाड़ियों के निर्माण में सीमेंट और स्टील बहुत ही आवश्यक घटक हैं। लेकिन ये दोनों उद्योग पर्यावरण को काफी नुकसान पहुंचाते हैं। सीमेंट के उत्पादन में प्रति वर्ष 2.3 अरब टन कार्बन डाईऑक्साइड का उत्सर्जन होता है जबकि लोहा और स्टील उत्पादन प्रति वर्ष 2.6 अरब टन कार्बन डाईऑक्साइड का उत्सर्जन करते हैं। ये वैश्विक कार्बन डाईऑक्साइड उत्सर्जन का क्रमश: 6.5 प्रतिशत और 7.0 प्रतिशत हैं।
इसका एक कारण तो यह है कि हम इन पदार्थों का उपयोग भारी मात्रा में करते हैं। देखा जाए तो स्वच्छ पानी के बाद कांक्रीट सबसे अधिक उपयोग होने वाला पदार्थ है। इसके अलावा, इनके उत्पादन की विधियां भी कार्बन आधारित हैं। इनमें जिन रासायनिक अभिक्रियाओं का उपयोग होता है उनमें कार्बन डाईऑक्साइड निकलती है। और तो और, निर्माण प्रक्रिया के लिए ज़रूरी उच्च तापमान हासिल करने के लिए जीवाश्म ईंधनों का दहन कार्बन डाईऑक्साइड का एक बड़ा स्रोत होता है।
ऐसे में सीमेंट और स्टील के उत्पादन एवं उपयोग के स्वच्छ तरीके खोजने की तत्काल आवश्यकता है। औद्योगिक मांग और ऊर्जा कीमतों में वृद्धि के बावजूद हमारे लिए 2050 तक नेट-ज़ीरो कार्बन उत्सर्जन लक्ष्य प्राप्त करना बहुत ज़रूरी है। यदि कम उत्सर्जन वाले भारी उद्योगों को फलते-फूलते देखना है तो इंफ्रास्ट्रक्चर, टेक्नॉलॉजी का हस्तांतरण और वित्तीय जोखिम कम करने के उपाय ज़रूरी होंगे।
नेचर के मार्च 2022 के अंक में प्रकाशित एक पर्चे में इम्पीरियल कॉलेज, लंदन के पौल फेनेल और जस्टिन ड्राइवर, साइमन फ्रेसर विश्वविद्यालय, कनाडा के क्रिस्टोफर बेटैल और कैलिफोर्निया विश्वविद्यालय, यूएसए के स्टीवन डेविस ने इस संदर्भ में कई सुझाव प्रस्तुत किए हैं जो स्टील को कार्बन उदासीन और सीमेंट को कार्बन सोख्ता बनाने में भूमिका निभा सकते हैं। प्रस्तुत है उनके पर्चे का सार।
1. नवीनतम तकनीकें
सभी उत्पादन संयंत्रों को सर्वोत्तम उपलब्ध तकनीक से सुसज्जित करना आवश्यक है। औद्योगिक संयंत्रों के तापरोधन में सुधार से 26 प्रतिशत ऊर्जा बचाई जा सकती है। बेहतर बॉयलर का उपयोग करके ऊर्जा खपत 10 प्रतिशत तक कम की जा सकती है। इसके साथ ही ऊष्मा विनिमय का उपयोग करने से शोधन प्रक्रिया की बिजली खपत को 25 प्रतिशत तक कम किया जा सकता है। अलबत्ता, एक समय के बाद किसी भी संयंत्र में सुधार करके ऊर्जा बचत की संभावना कम होती जाती है। वर्तमान के सबसे कुशल सीमेंट संयंत्र उन्नत प्रौद्योगिकियों को अपनाकर मात्र 0.04 प्रतिशत ऊर्जा की बचत कर पाएंगे। यानी कुछ और करने की ज़रूरत है।
2. कम उपयोग
एक ही काम के लिए कम मात्रा में स्टील और सीमेंट का उपयोग किया जा सकता है। फिलहाल दुनिया में प्रति व्यक्ति प्रति वर्ष 530 किलोग्राम सीमेंट और 240 किलोग्राम स्टील का उत्पादन हो रहा है। इंटरनेशनल एनर्जी एजेंसी (आईए) के अनुसार यदि भवन निर्माण संहिता और आर्किटेक्ट्स, इंजीनियर्स तथा ठेकेदारों के प्रशिक्षण में कुछ महत्वपूर्ण बदलाव किए जाएं, तो सीमेंट की मांग को 26 प्रतिशत और स्टील की मांग को 24 प्रतिशत तक कम किया जा सकता है। कई भवन निर्माण संहिताएं सुरक्षा के लिए ज़रूरत से ज़्यादा डिज़ाइन का सहारा लेती हैं। यदि आधुनिक सामग्रियों और बढ़िया कंप्यूटर मॉडलिंग का उपयोग करके डिज़ाइन तैयार की जाए तो कम से कम संसाधनों से काम चल सकता है। इसके अलावा, कम कार्बन पदचिन्ह वाली वैकल्पिक सामग्री का भी उपयोग किया जा सकता है। जैसे वाहनों में स्टील के स्थान पर एल्युमीनियम। इसके लिए काम करने के पुराने तरीकों को बदलना होगा।
3. तकनीकी नवाचार
पारंपरिक स्टील उत्पादन में कार्बन की महत्वपूर्ण भूमिका है। ब्लास्ट फर्नेस (वात भट्टी) में ईंधन के रूप में कोक (एक किस्म का कोयला) का उपयोग किया जाता है जिसमें लौह खनिज को 2300 डिग्री सेल्सियस तापमान पर धात्विक लोहे में परिवर्तित किया जाता है। कोक के जलने पर कार्बन मोनोऑक्साइड बनती है जो अयस्क को लोहे और कार्बन डाईऑक्साइड में बदल देती है। इसके बाद लोहे को कोयला-भट्टी या कभी-कभी विदुयत भट्टी में परिष्कृत कर स्टील प्राप्त किया जाता है। इस प्रक्रिया में प्रति टन स्टील 1800 किलोग्राम से अधिक कार्बन डाईऑक्साइड पैदा होती है।
वैसे, अयस्क से लोहा प्राप्त करने के लिए अन्य पदार्थों का उपयोग भी किया जा सकता है। गौरतलब है कि विश्व का लगभग 5 प्रतिशत स्टील डायरेक्ट रिड्यूस्ड आयरन (डीआरआई) प्रक्रियाओं से बनाया जाता है जिनमें कोक की आवश्यकता नहीं होती है। इसके लिए आम तौर पर हाइड्रोजन और कार्बन मोनोऑक्साइड (मीथेन अथवा कोयले से प्राप्त) का उपयोग किया जाता है। इसके साथ-साथ यदि विद्युत भट्टी के लिए नवीकरणीय बिजली का उपयोग किया जाए तो ऐसे स्टील संयंत्र कोक आधारित संयंत्र की तुलना में 61 प्रतिशत कम कार्बन डाईऑक्साइड पैदा करते हैं।
और तो और, डीआरआई के लिए केवल हाइड्रोजन का उपयोग किया जाए तो उत्सर्जन को 50 किलोग्राम प्रति टन स्टील या उससे कम किया जा सकता है। कुछ कंपनियां इस तरह के संयंत्र आज़मा रही हैं।
इस प्रक्रिया की सबसे बड़ी चुनौती यह है कि इसके लिए भारी मात्रा में हाइड्रोजन की आवश्यकता होती है। समस्त स्टील का उत्पादन इस तरीके से करने के लिए वैश्विक हाइड्रोजन उत्पादन को वर्तमान 6 करोड़ टन से बढ़ाकर से 13.5 करोड़ टन प्रति वर्ष करना होगा। वर्तमान में सबसे सस्ती हाइड्रोजन प्राकृतिक गैस से प्राप्त होती है जिससे कार्बन डाईऑक्साइड का उत्सर्जन होता है। इसका एक हरित विकल्प विद्युत-अपघटन की मदद से पानी से हाइड्रोजन प्राप्त करने का है लेकिन वह 2.5 गुना महंगा है। संयंत्रों की संख्या बढ़ेगी तो लागत कम हो सकती है।
अन्य विकल्प भी आज़माए जा सकते हैं। वर्ष 2004 में 15 युरोपीय देशों की 48 कंपनियों और संगठनों के एक संघ ने विभिन्न विकल्पों का मूल्यांकन किया। टाटा स्टील ने 2010 में नीदरलैंड में एक उन्नत स्टील उत्पादन प्रक्रिया वाला पायलट संयंत्र तैयार किया था, जो है तो कोयला आधारित लेकिन इसमें कार्बन को आसानी से थामा जा सकता है। फिलहाल हरित हाइड्रोजन की गिरती कीमत से टाटा हाइड्रोजन आधारित डीआरआई को अपनाने पर विचार कर रहा है। हाइड्रोजन का एक अच्छा विकल्प विद्युत-विच्छेदन के माध्यम से लोहा प्राप्त करने का है और इस पर काम चल रहा है।
4. नए प्रकार का सीमेंट
साधारण पोर्टलैंड सीमेंट का उत्पादन चूना पत्थर के कैल्सीनेशन से शुरू होता है। इस प्रकिया में चूना पत्थर को 850 डिग्री सेल्सियस से अधिक तापमान पर गर्म करने पर वह चूना और कार्बन डाईऑक्साइड में परिवर्तित हो जाता है। चूने को रेत और मिट्टी के साथ मिलाकर 1450 डिग्री सेल्सियस तक भट्टी में पकाने पर क्लिंकर बनता है। जिसमें कुछ अन्य पदार्थ मिलाकर सीमेंट बनाया जाता हैं। लगभग 60 प्रतिशत कार्बन उत्सर्जन कैल्सीनेशन के दौरान होता है। शेष उत्सर्जन ईंधन के दहन से होता है। कुल मिलाकर, एक औसत संयंत्र में प्रति टन सीमेंट 800 किलोग्राम कार्बन डाईऑक्साइड का उत्सर्जन होता है। उन्नत संयंत्र में यह मात्र 600 किलोग्राम होता है।
गौरतलब है कि चूना पत्थर के बिना भी सीमेंट बनाया जा सकता है। उदाहरण के लिए मैग्नीशियम ऑक्सीक्लोराइड सीमेंट (सॉरेल) 1867 से मौजूद रहा है लेकिन पानी के प्रति कम सहनशीलता के कारण इसका व्यावसायीकरण नहीं हो पाया है। फिलहाल सीमेंट के कई प्रकारों को परखा जा रहा है। निर्माण में इनका उपयोग करने के लिए भवन निर्माण कोड, डिज़ाइन और तौर तरीकों को बदलना होगा, जिसमें समय लगेगा।
एक विकल्प क्लिंकर के स्थान पर कोई अन्य टिकाऊ सामग्री हो सकती है। यह सामग्री वात भट्टी का अपशिष्ट (स्लैग) और कोयला बिजलीघरों की राख हो सकती है। लेकिन जीवाश्म ईंधनों को चरणबद्ध तरीकों से खत्म करने पर इन सामग्रियों की प्राप्ति मुश्किल हो जाएगी। फिलहाल, शोधकर्ता अन्य विकल्प खोजने के प्रयास कर रहे हैं जिनमें लोहे और स्टील के रीसायकल संयंत्रों का स्लैग शामिल है।
एक और उदाहरण लाइमस्टोन कैलसाइन्ड क्ले सीमेंट (एलसी3) है। इसका जल्द ही व्यावसायीकरण संभव है। एक विकल्प यह है कि क्लिंकर की जगह अन्य सस्टेनेबल पदार्थों का उपयोग किया जाए। कई कंपनियों ने अपनी नेट-ज़ीरो रणनीतियों में एलसी3 को शामिल किया है।
5. ईंधन में बदलाव
यह विचार लुभावना लगता है कि स्टील के लिए, कोयले और कोक की जगह लकड़ी के कोयले या अन्य जैव-पदार्थों का उपयोग किया जाए। लेकिन इसमें कई चुनौतियां हैं। ऊर्जा के लिए जैव-पदार्थों में वृद्धि का कृषि भूमि की ज़रूरत के साथ टकराव होगा और सारे जैव-पदार्थ का उत्पादन निर्वहनीय नहीं होता। कोक की तुलना में लकड़ी का कोयला वात भट्टी के लिए उपयुक्त नहीं होता है। लिहाज़ा स्टील प्रसंस्करण के ‘तकनीकी नवाचार’ शीर्षक में दिए गए सुझावों पर अमल ही शायद बेहतर होगा।
वैसे सीमेंट के लिए नगर पालिका का ठोस अपशिष्ट वैकल्पिक ईंधन के रूप में उपयोग किया जा सकता है। भट्टी का ऊंचा तापमान ज़हरीले पदार्थों को नष्ट कर सकता है और राख को क्लिंकर में शामिल किया जा सकता है। युनाइटेड किंगडम स्थित मेक्सिकन कंपनी सीमेक्स एनर्जी के सीमेंट संयंत्रों की 57 प्रतिशत ऊर्जा इन वैकल्पिक ईंधनों से प्राप्त होती है जबकि यूके आधारित कंपनी हैनसन 52 प्रतिशत वैकल्पिक ईंधन की खपत करता है। इस रणनीति को उपयुक्त नियम-कानून बनाकर राष्ट्र स्तर पर प्रोत्साहित किया जाना चाहिए।
6. कार्बन कैप्चर
सीसीएस तकनीक यानी कार्बन डाईऑक्साइड को कैद करके भंडारित करने की तकनीक सीमेंट और स्टील संयंत्रों के उत्सर्जन को कम करने के लिए अनिवार्य होगी। सीसीएस का उपयोग कई देशों में किया जा रहा है। नॉर्वे की सरकारी कंपनी एक्विनार 1990 के दशक से सीसीएस परियोजना के तहत प्रति वर्ष 10 लाख टन कार्बन डाईऑक्साइड को धरती में दफन कर रही है। लेकिन इस तकनीक का पर्याप्त उपयोग नहीं किया गया है। अब तक वैश्विक उत्सर्जन का केवल 0.1 प्रतिशत ही कैप्चर करके भूमिगत किया गया है। कुछेक चुनिंदा संयंत्र सीसीएस का परीक्षण कर रहे हैं। फिलहाल आबू धाबी में एक आधुनिक डीआरआई स्टील संयंत्र 2016 से सीसीएस का उपयोग कर रहा है। सीसीएस को बढ़ाने की ज़रूरत है।
इसमें गैस को संपीड़ित और संग्रहित करने की लागत को कम करने के लिए कार्बन डाईऑक्साइड 99.9 प्रतिशत से अधिक शुद्ध होना अनिवार्य है। एक सामान्य स्टील और सीमेंट संयंत्र की चिमनी से 30 प्रतिशत कार्बन डाईऑक्साइड और बाकी नाइट्रोजन और भाप निकलती है। एक विकल्प है कि ईंधन को ऑक्सीजन और रीसायकल गैसों के मिश्रण में जलाया जाए ताकि अपेक्षाकृत शुद्ध कार्बन डाईऑक्साइड प्राप्त हो। यह काफी मुश्किल है क्योंकि इसके लिए घूमती-तपती भट्टी को सील करना ज़रूरी होता है।
कैल्सिनेशन प्रक्रिया से कार्बन डाईऑक्साइड को अलग करने का एक अन्य तरीका चूना पत्थर को परोक्ष ढंग से गर्म करना है (जैसे दीवार के ज़रिए) ताकि चूना पत्थर से निकलने वाली गैस और ईंधन दहन का उत्सर्जन अलग-अलग रहें। चूना पत्थर से निकलने वाला उत्सर्जन काफी शुद्ध होता है जिससे सीसीएस की लागत में कमी आती है। बेल्जियम और जर्मनी में LEILAC1 और 2 परियोजनाएं इसका परीक्षण कर रही हैं। LEILAC2 20 प्रतिशत (लगभग एक लाख टन प्रति वर्ष) उत्सर्जन को कैप्चर कर रही है।
इसके अलावा भारी उद्योगों को समूहों में बनाने से हाइड्रोजन उत्पादन के लिए ऊष्मा, सामग्री और बुनियादी ढांचे और कार्बन डाईऑक्साइड का संग्रहण और निपटान साझा हो सकता है। ऐसे क्लस्टर यूके, डेनमार्क, नीदरलैंड और नॉर्वे में तैयार हो रहे हैं।
7. कॉन्क्रीट में कार्बन संग्रहण
कॉन्क्रीट तैयार करने के लिए सीमेंट में पानी के साथ रेत और गिट्टी मिलाई जाती हैं। इसमें पानी कुछ रासायनिक अभिक्रियाएं शुरू करता है जो सामग्री को सख्त बना देती हैं, जोड़ देती हैं। इसमें कार्बन डाईऑक्साइड मिलाने से सीमेंट की मज़बूती बढ़ती है। वज़न के हिसाब से 1.3 प्रतिशत कार्बन डाईऑक्साइड कठोरता को लगभग 10 प्रतिशत तक बढ़ा देती है। ऐसा करने से निर्माण के लिए सीमेंट की ज़रूरत कम हो जाती है और कुल उत्सर्जन में 5 प्रतिशत तक की कमी आती है।
कॉन्क्रीट में कार्बन कैप्चर अनुसंधान का सक्रिय क्षेत्र है। कनाडा स्थित कार्बनक्योर जैसी कंपनियां बड़े पैमाने पर कार्बन डाईऑक्साइड को कॉन्क्रीट में इंजेक्ट कर रही हैं। उन्होंने अब तक दो लाख टन कार्बनक्योर कॉन्क्रीट बेचा किया है जिससे डाईऑक्साइड उत्सर्जन में 1,32,000 टन की कमी आई है।
सीमेंट और कॉन्क्रीट दोनों हवा से कार्बन डाईऑक्साइड अवशोषित करते हैं जो कैल्शियम आधारित पदार्थों को वापिस चूना पत्थर में परिवर्तित कर देती है। सिद्धांतत: इस प्रक्रिया से सीमेंट निर्माण के दौरान उत्सर्जित कार्बन डाईऑक्साइड का लगभग आधा हिस्सा फिर से अवशोषित किया जा सकता है। लेकिन इसके लिए कॉन्क्रीट के कणों को पीसकर महीन बनाना होगा ताकि कार्बन डाईऑक्साइड अच्छे से फैल सके। यह प्रक्रिया काफी महंगी है और इसके लिए ऊर्जा की भी ज़रूरत होती है। वैसे इसमें कितनी कार्बन डाईऑक्साइड सोखी जाएगी यह काफी अनिश्चित होता है और इसलिए इसे यूएन जलवायु परिवर्तन कार्यों की सूची में स्थान नहीं मिला है।
8. स्टील का पुनर्चक्रण
इलेक्ट्रिक आर्क फर्नेस (ईएएफ) का उपयोग करके स्टील का पुनर्चक्रण किया जा सकता है। वर्तमान में स्टील उत्पादन का एक चौथाई भाग पुनर्चक्रित स्क्रैप से प्राप्त होता है। वैश्विक स्तर पर 2050 तक पुनर्चक्रित स्टील का उत्पादन दुगना होने की संभावना है। इससे कार्बन उत्सर्जन आज की तुलना में 20-25 प्रतिशत तक कम किया जा सकेगा।
स्टील का लगातार पुनर्चक्रण वर्तमान में संभव नहीं है। ऐसा करने से उसमें अवांछनीय यौगिक, विशेषकर तांबा, इकट्ठा होने लगते हैं। स्क्रैप की बेहतर छंटाई करके और उत्पादों को नया रूप देकर इस प्रक्रिया को धीमा किया जा सकता है।
9. सब्सिडी
उपरोक्त आठ बिंदुओं का प्रभाव काफी विशाल हो सकता है। लेकिन कम कार्बन उत्सर्जन वाले भारी उद्योगों को बड़े पैमाने पर शामिल करने के लिए आर्थिक बाधाओं का सामना करना होगा। स्टील के लिए हाइड्रोजन आधारित डीआरआई संयंत्रों और सीमेंट के लिए सीसीएस सुविधाएं पायलट से लेकर शुरुआती व्यावसायिक चरणों तक मौजूद हैं। इनको बढ़ाना काफी महंगा और जोखिम भरा है। कम कार्बन वाले उत्पादों को प्रतिस्पर्धा में नुकसान होता है। अधिकांश निर्माण कार्य विकासशील देशों में हो रहा है। अत: उनके साथ टेक्नॉलॉजी साझा करने और वित्तीय जोखिमों को कम करने की प्रणालियां लागू करने की आवश्यकता है। जीवाश्म ईंधन को जैव-पदार्थों या हाइड्रोजन से बदलने या सीसीएस के लिए युरोपीन युनियन एमिशन ट्रेडिंग स्कीम (ईटीएस) के तहत कदम उठाना एक अच्छा विचार है। लेकिन शायद सरकार की ओर से सब्सिडी ज़्यादा प्रभावी हो सकती है। सीसीएस के साथ पूर्ण कार्बन-मुक्ति से पोर्टलैंड सीमेंट की लागत दुगनी होने की उम्मीद है। शून्य-उत्सर्जन स्टील की लागत सामान्य स्टील की तुलना में 20-40 प्रतिशत अधिक होने की संभावना है। इस सबकी क्षतिपूर्ति के लिए सब्सिडी ज़रूरी होगी। (स्रोत फीचर्स)
नोट: स्रोत में छपे लेखों के विचार लेखकों के हैं। एकलव्य का इनसे सहमत होना आवश्यक नहीं है।
Photo Credit : https://media.nature.com/lw800/magazine-assets/d41586-022-00758-4/d41586-022-00758-4_20224532.jpg